Si Arthena concentre ses activités sur la Suisse romande, elle ne s'interdit pas - au hasard des rencontres et des voyages - de rapporter d'ailleurs de belles histoires. Car les artisans et les métiers d'art ne connaissent - heureusement! - pas les frontières.
MANUFACTURE DE SOULIERS
Crockett & Jones | Northampton (Angleterre)
Découvrir de l’intérieur la manufacture dirigée par la cinquième génération de descendants des fondateurs, c’est plonger dans un savoureux mélange de tradition manufacturière et d’indispensable modernisation. C’est aussi l’assurance de ne plus jamais regarder les chaussures de la même manière.
En matière de beaux souliers, à chacun sa religion. De fabrication italienne, française ou encore anglaise, il y en a pour tous les goûts et toutes les bourses. Il n’en reste pas moins que pour nombre d’amateurs de formes aussi classiques qu’intemporelles, le « made in England » demeure une valeur sûre. La région de Northampton en particulier constitue le berceau historique de la botterie anglaise, en raison de la présence par le passé de nombreuses tanneries qui trouvaient là du bétail et de l’eau en abondance, tous deux indispensables à leur activité.
Située à quelque 100 kilomètres au nord de Londres, Northampton - détruite à la fin du XVIIème siècle par un important incendie - n’offre à vrai dire pas un grand intérêt touristique. On s’y rend essentiellement pour découvrir des savoir-faire d’exception, hérités de générations d’artisans qui se sont succédés dans de célèbres manufactures. Parmi celles-ci, Crockett & Jones, fondée en 1879.
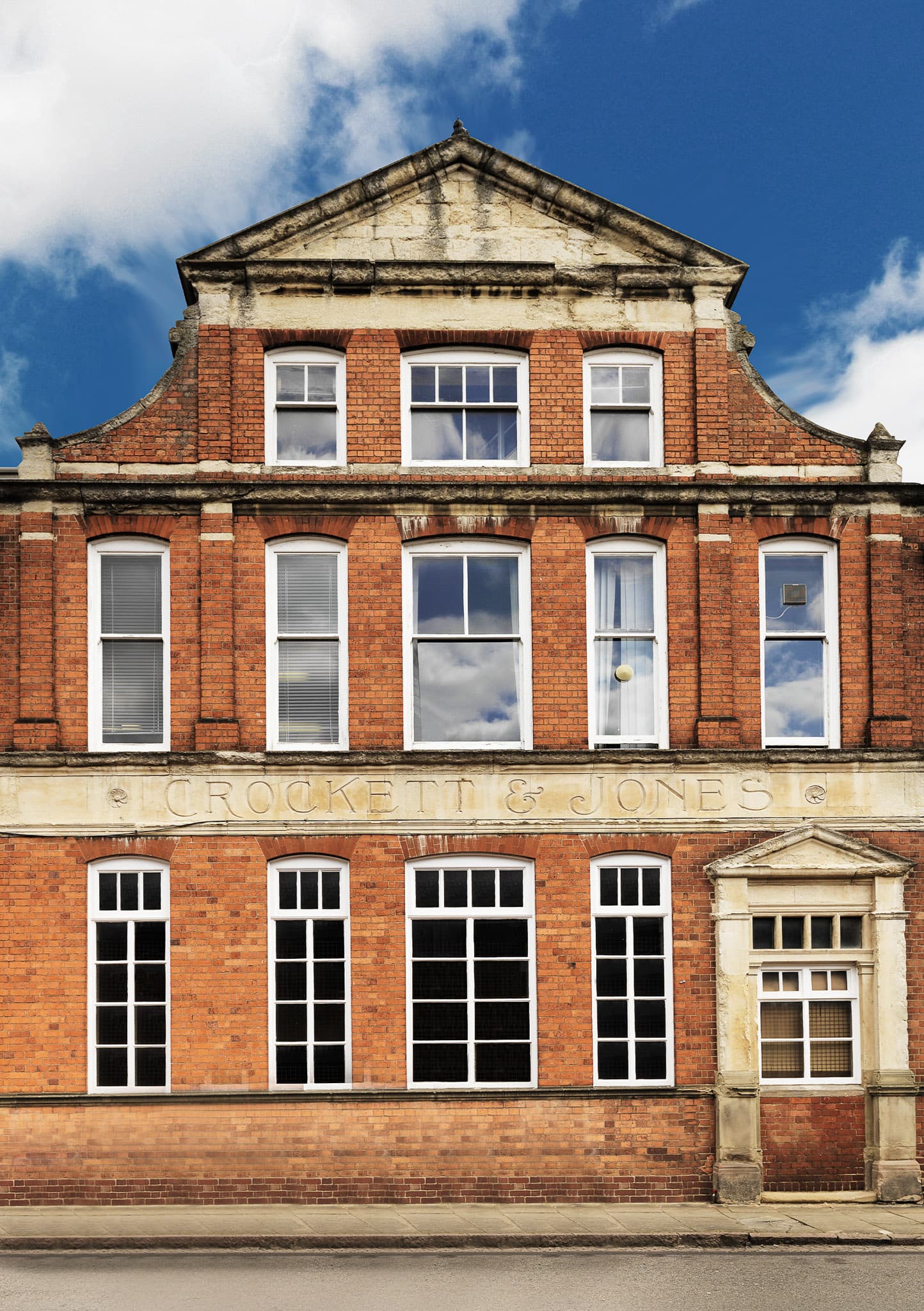
Le site de production compte trois vastes bâtiments à l’architecture Art déco, typique des années 30 durant lesquelles ils furent édifiés pour répondre à la croissance de l’entreprise. Difficile de deviner depuis la paisible Perry Street l’intensité de l’activité qui est déployée à l’intérieur de ces édifices désormais classés monuments historiques. Dans la chaleur et le bruit bien souvent, plus de 300 collaborateurs s’affairent là, chacun à son poste et selon un horaire scandé par une sonnerie tonitruante.
220 à 250 opérations manuelles successives - en fonction de la complexité du modèle - sont nécessaires à la production traditionnelle d’une chaussure avec un montage Goodyear, une technique d’assemblage qui remonte au XIXème. En pleine activité, la manufacture s’apparente à une véritable ruche. Avec plus de 700 références différentes au catalogue et en moyenne autant de paires qui sortent quotidiennement des ateliers, la gestion de l’ensemble des paramètres de production nécessite une attention de tous les instants. « D’autant que - comme le souligne Nicholas Jones, en charge de la fabrication - huit semaines séparent la première de la dernière étape. » De quoi allègrement y perdre son… flegme britannique!
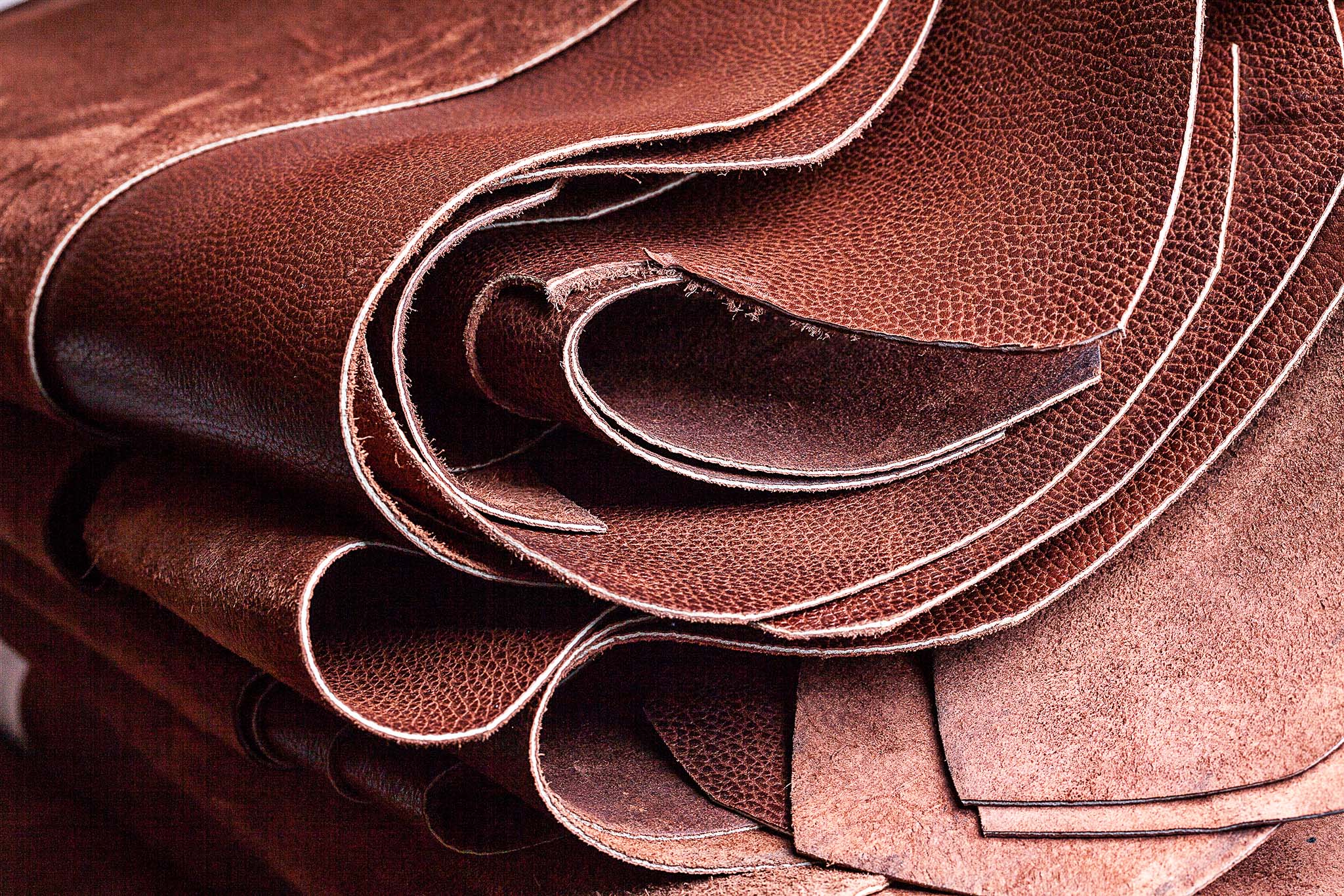
La genèse d’un soulier de qualité débute par la sélection rigoureuse du cuir, rendue de plus en plus compliquée notamment par une consommation de viande en baisse en Europe. « Nous ne nous approvisionnons qu’auprès des meilleures tanneries, en achetant la qualité supérieure. Les relations que nous entretenons de longue date avec elles et la confiance réciproque nous permettent d’obtenir ce qu’aucun nouvel acteur sur le marché ne pourrait espérer, même en y mettant le prix. Mais la situation est critique, car l’offre ne suit plus la demande », précise Jonathan Jones, frère de Nicholas et directeur général de l’entreprise.
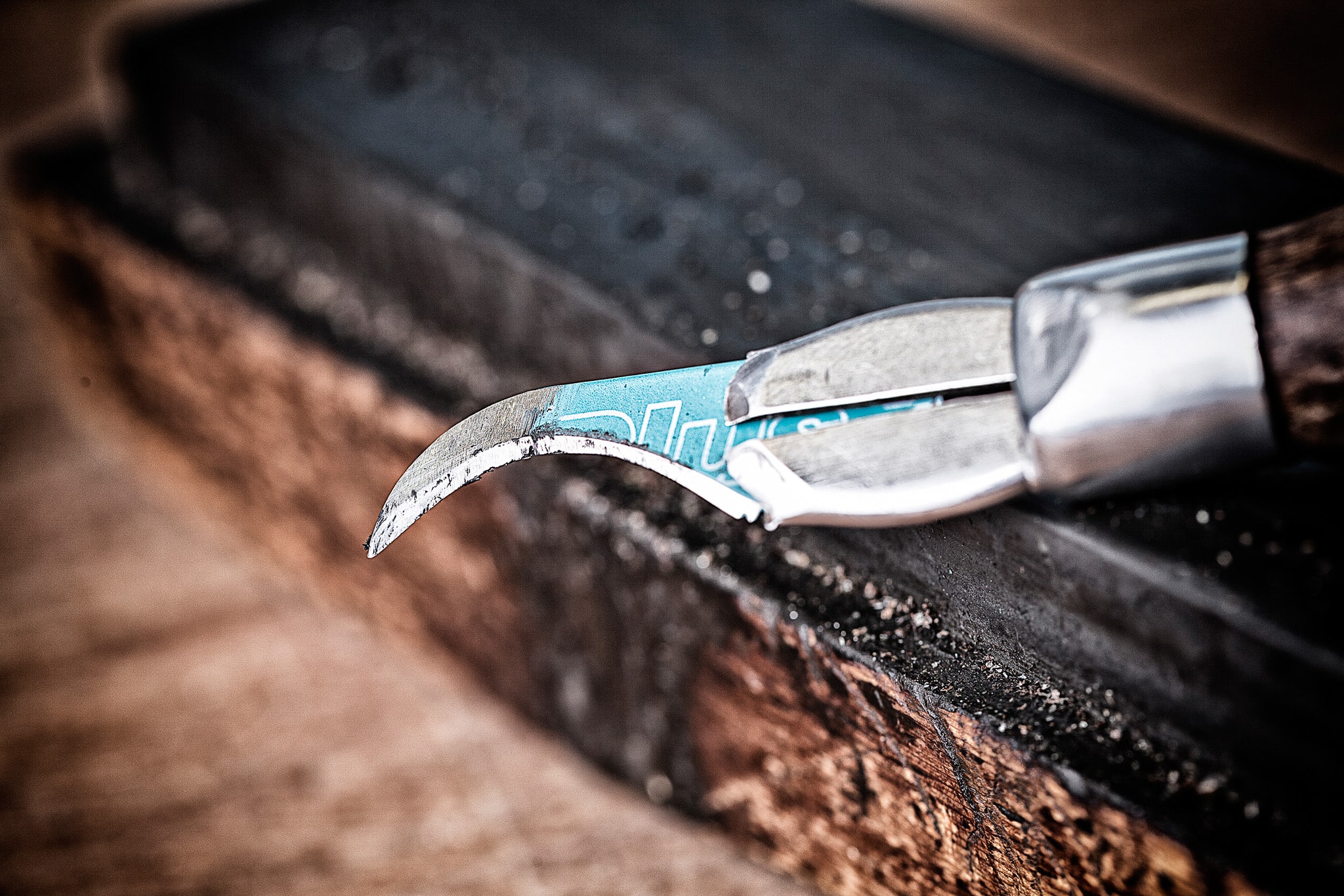
La fabrication à proprement parler débute - une fois le modèle dessiné et le patronage réalisé - par la coupe de la tige, soit la partie supérieure du soulier. Une étape cruciale, puisque revient au découpeur la responsabilité de l’examen minutieux de la peausserie afin d’y déceler la moindre imperfection qui, immanquablement, affecterait la qualité finale de la réalisation. Le savoir-faire de l’artisan permet à ce stade de tirer profit au mieux de la matière première, en minimisant les pertes.
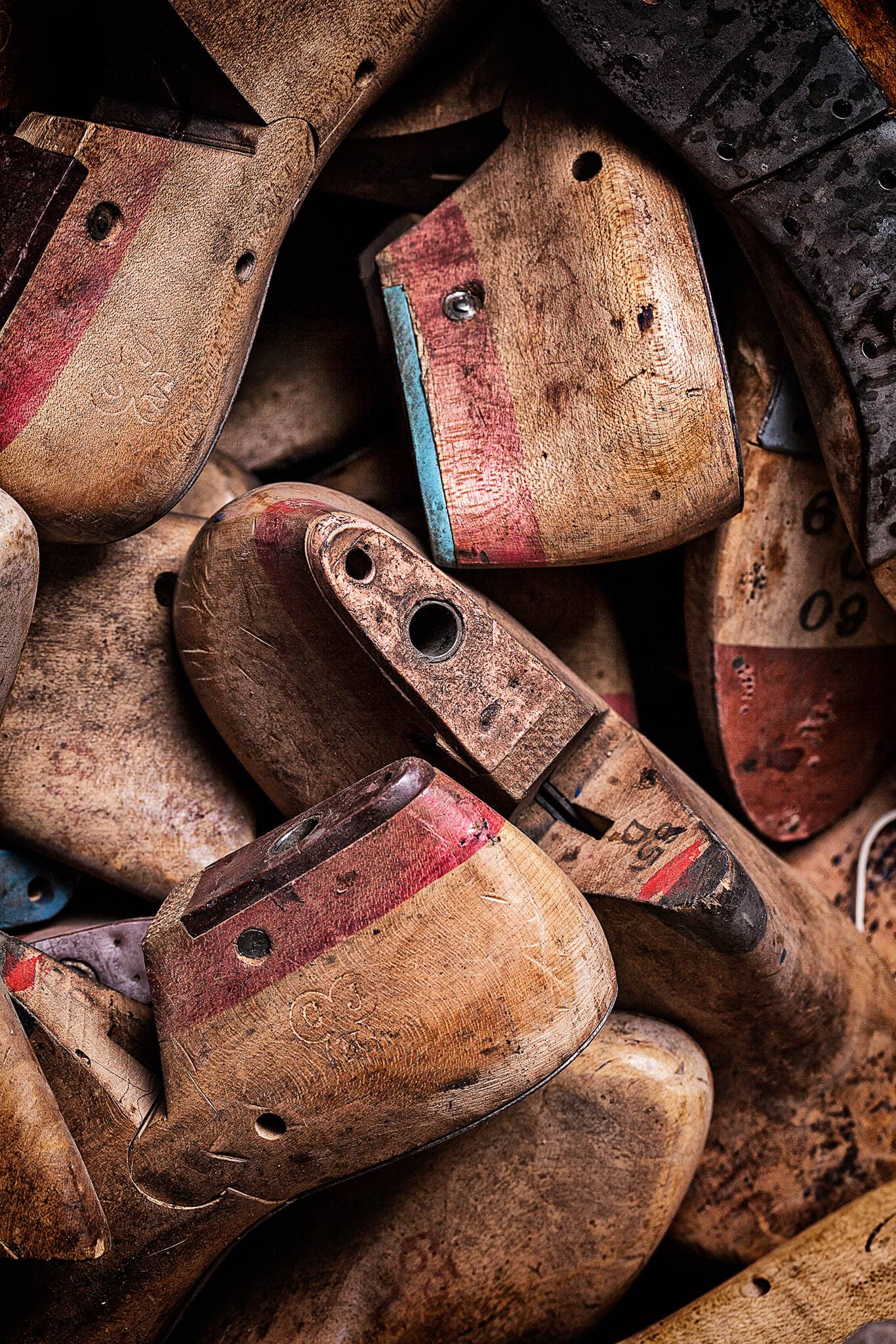
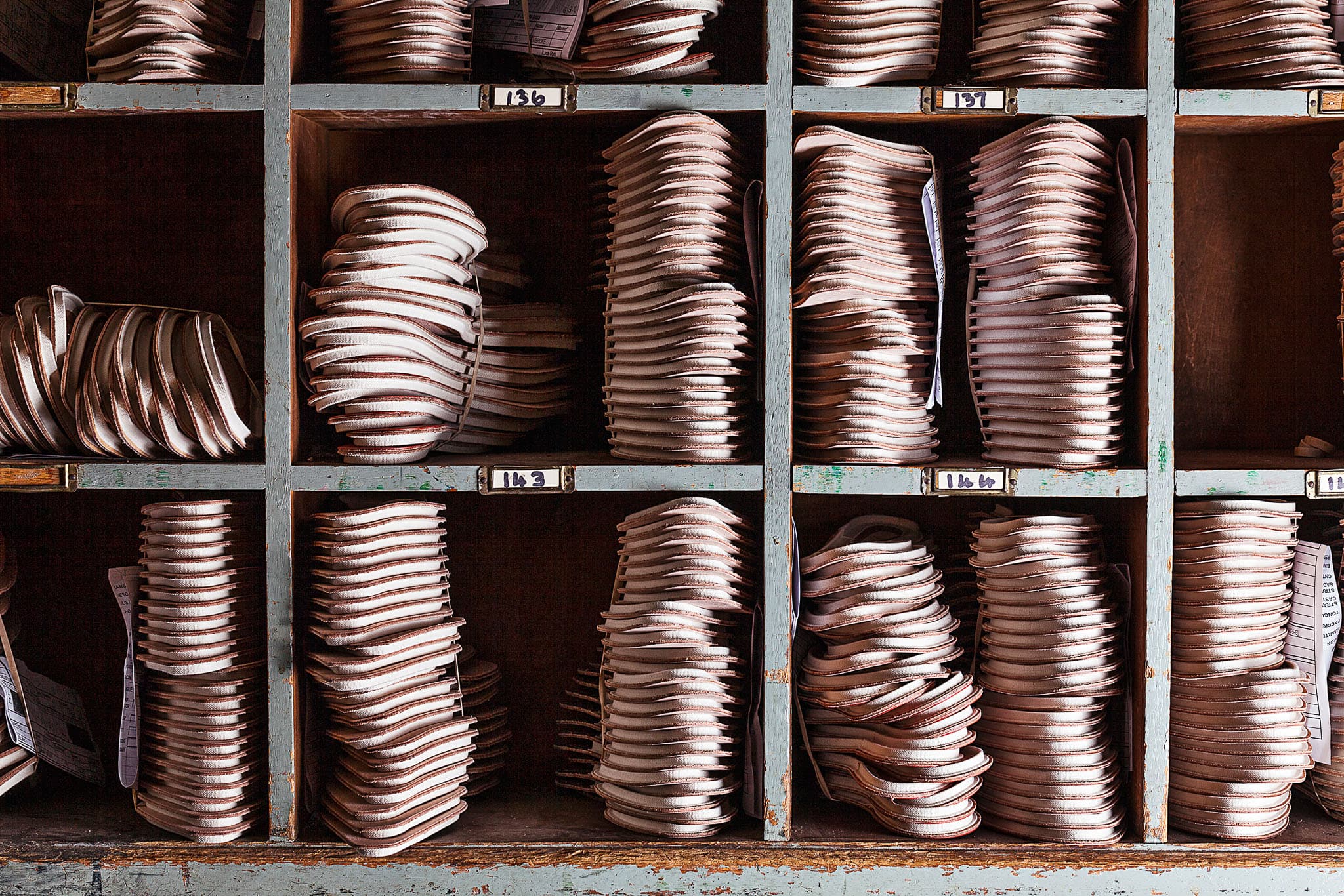
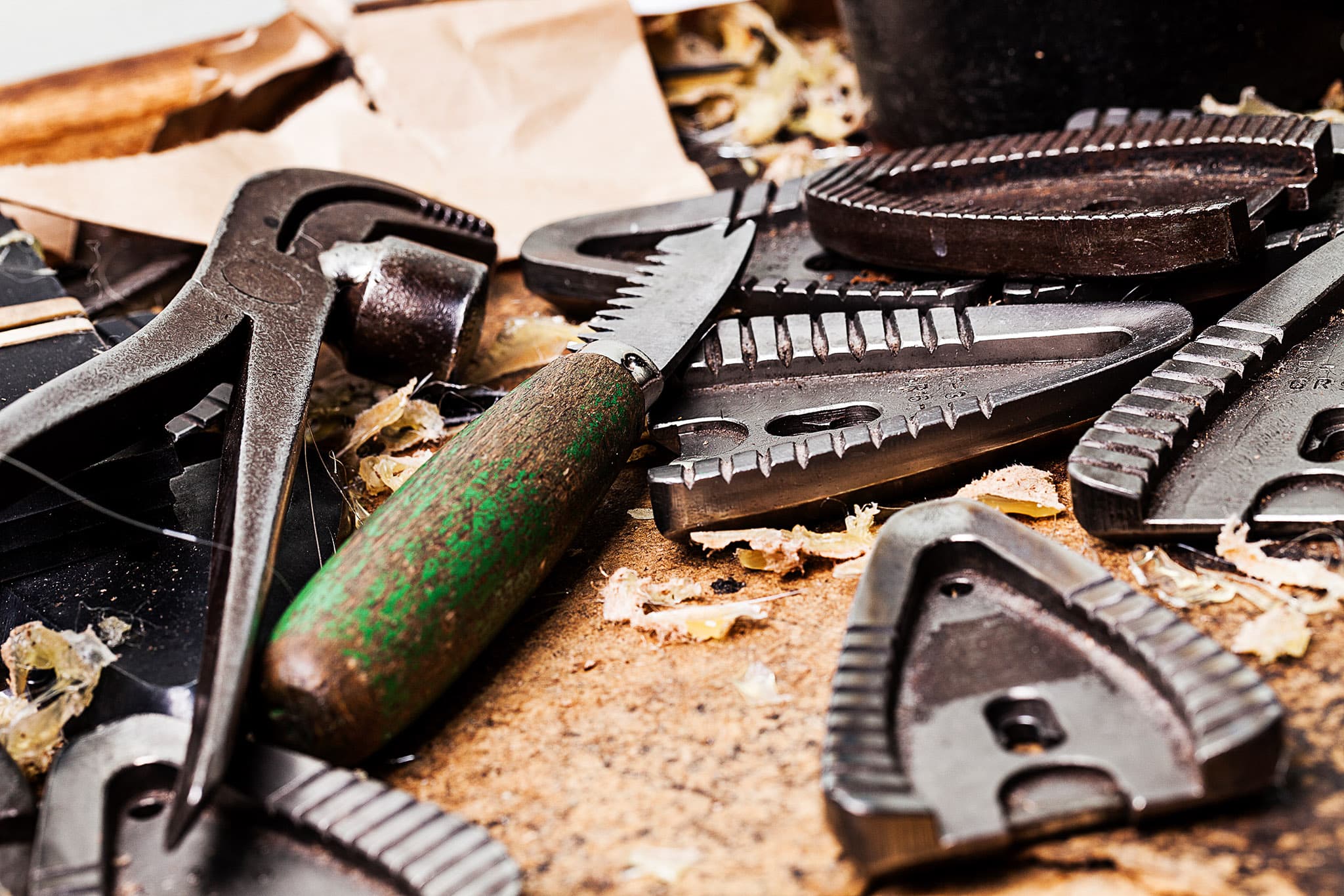
Vient ensuite l’atelier de confection de la tige, qui voit cette dernière teinte, ornementée puis cousue puisque, bien souvent, elle est constituée de plusieurs pièces de cuir. On devine déjà l’âme du produit final, alors même qu’il n’apparaît qu’en deux dimensions. La confection de la partie inférieure de la chaussure, composée de plusieurs éléments superposés appelés semelage, peut alors commencer.
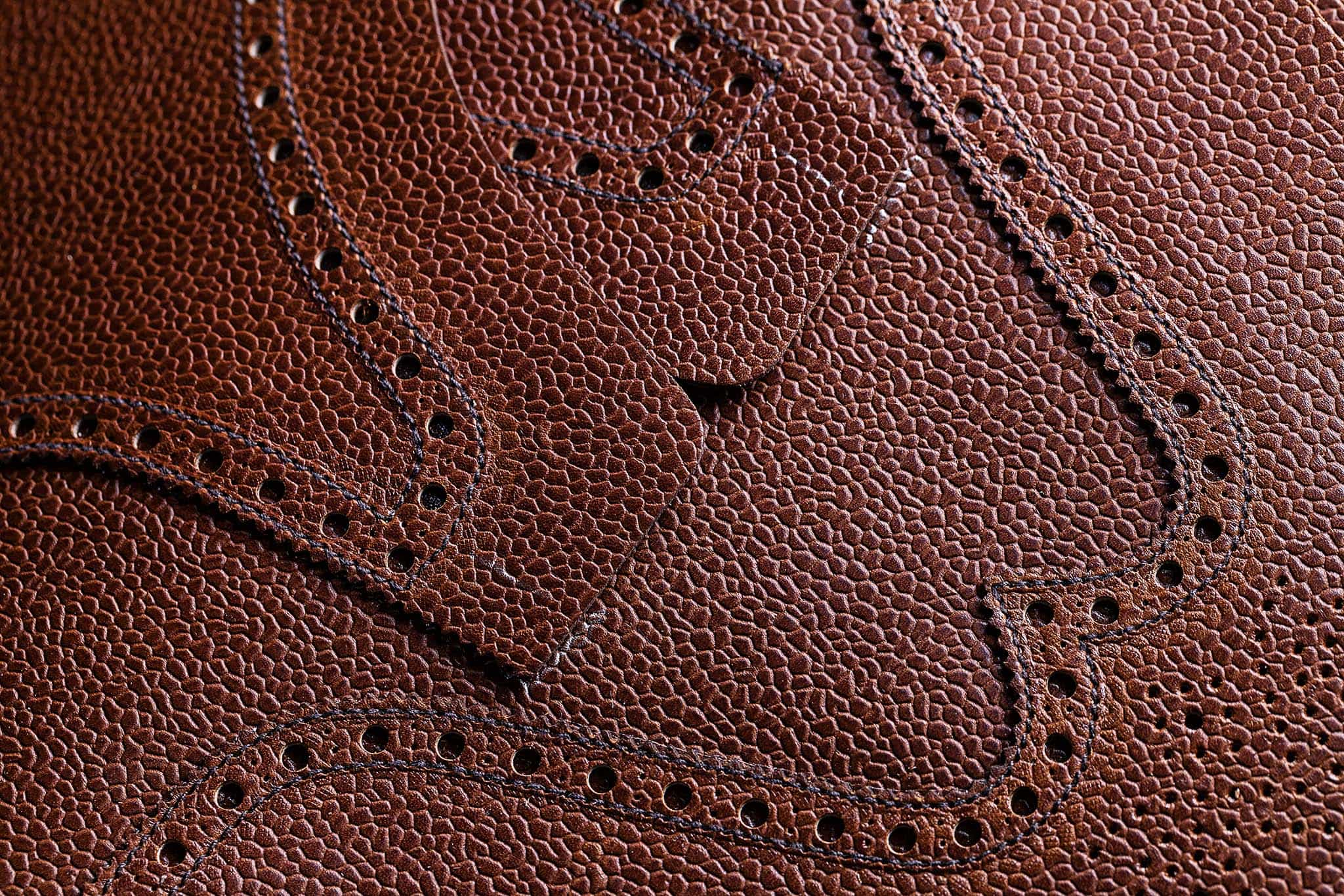
Cette étape consiste à découper dans d’épaisses bandes de cuir la partie supérieure de la semelle. Pour cela, l’ouvrier actionne une puissante presse qui vient écraser des formes métalliques tranchantes posée sur la matière. Le résultat? Une « première », ainsi nommée en raison de son positionnement tout en haut du semelage, en contact direct avec la tige. C’est grâce à un bourrelet de quelques millimètres - le « mur de montage » - cousu sur la « première » que, par la suite, les parties supérieures et inférieures de la chaussure pourront être solidarisées.
Juste le temps de reprendre son souffle avant de passer au montage, quelques dizaines de mètres plus loin. La tige doit encore prendre ses galbes, passer de deux à trois dimensions. Positionnée sur une forme en plastique dur, puis fixée sur celle-ci à l’aide de clous, une machine pneumatique l’étire fortement de manière à lui faire épouser parfaitement le support sur laquelle elle se trouve. Le cuir a de la mémoire; la forme est ainsi définitivement acquise. L’assemblage peut alors avoir lieu grâce à une mince bande de cuir, la trépointe.
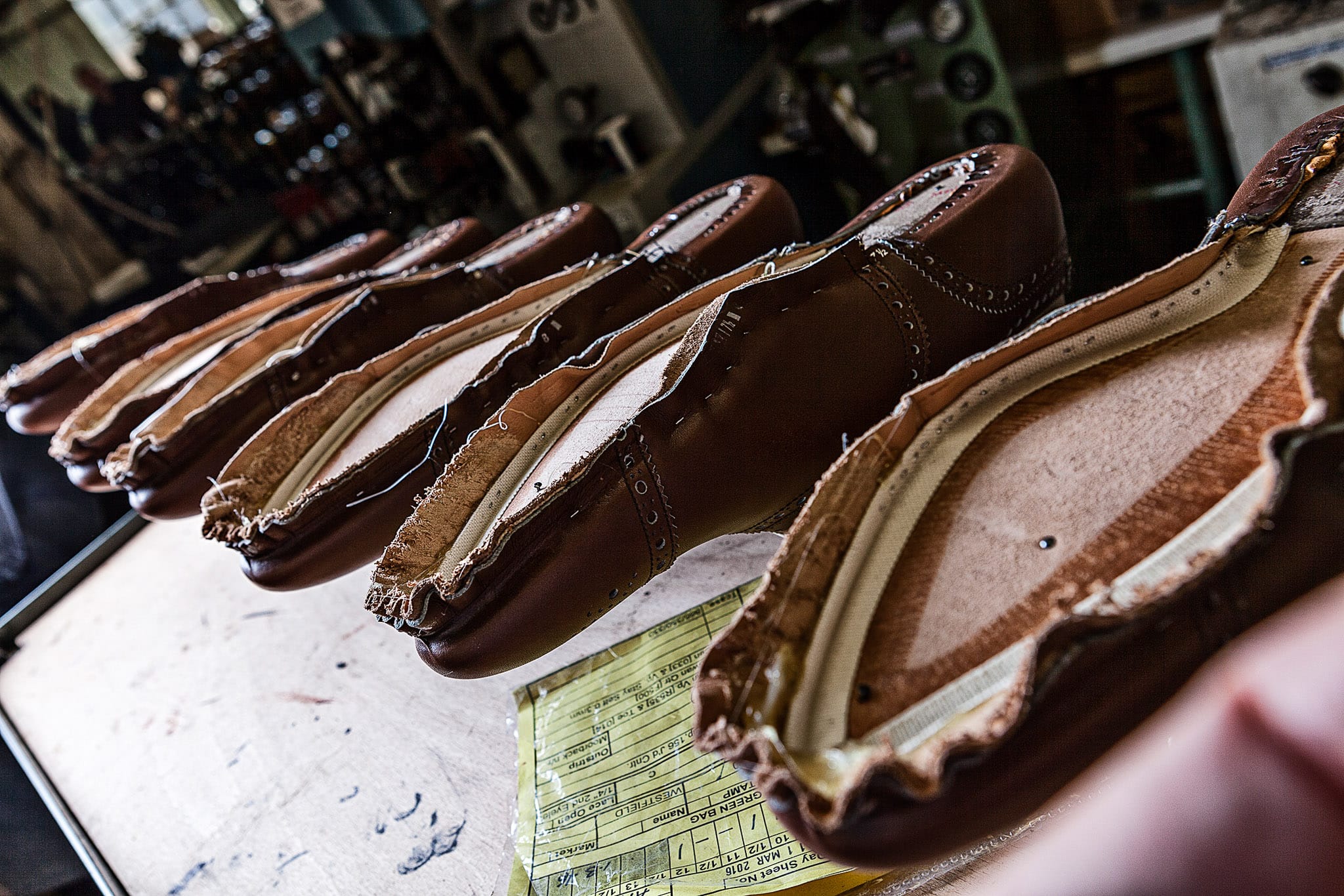
Dans le dernier atelier, celui dit de finition, des artisans s’appliquent à fixer les talons, les ajuster et les poncer avant de les teindre et d’appliquer sur le pourtour de la semelle de la cire chaude afin d’assurer à l’ensemble étanchéité et brillance. C’est enfin au tour des tiges d’être bichonnées par des mains expertes. Après deux mois en moyenne, les chaussures atteignent le terme d’un processus de fabrication certes long et complexe, mais garant du respect des plus hautes exigences.
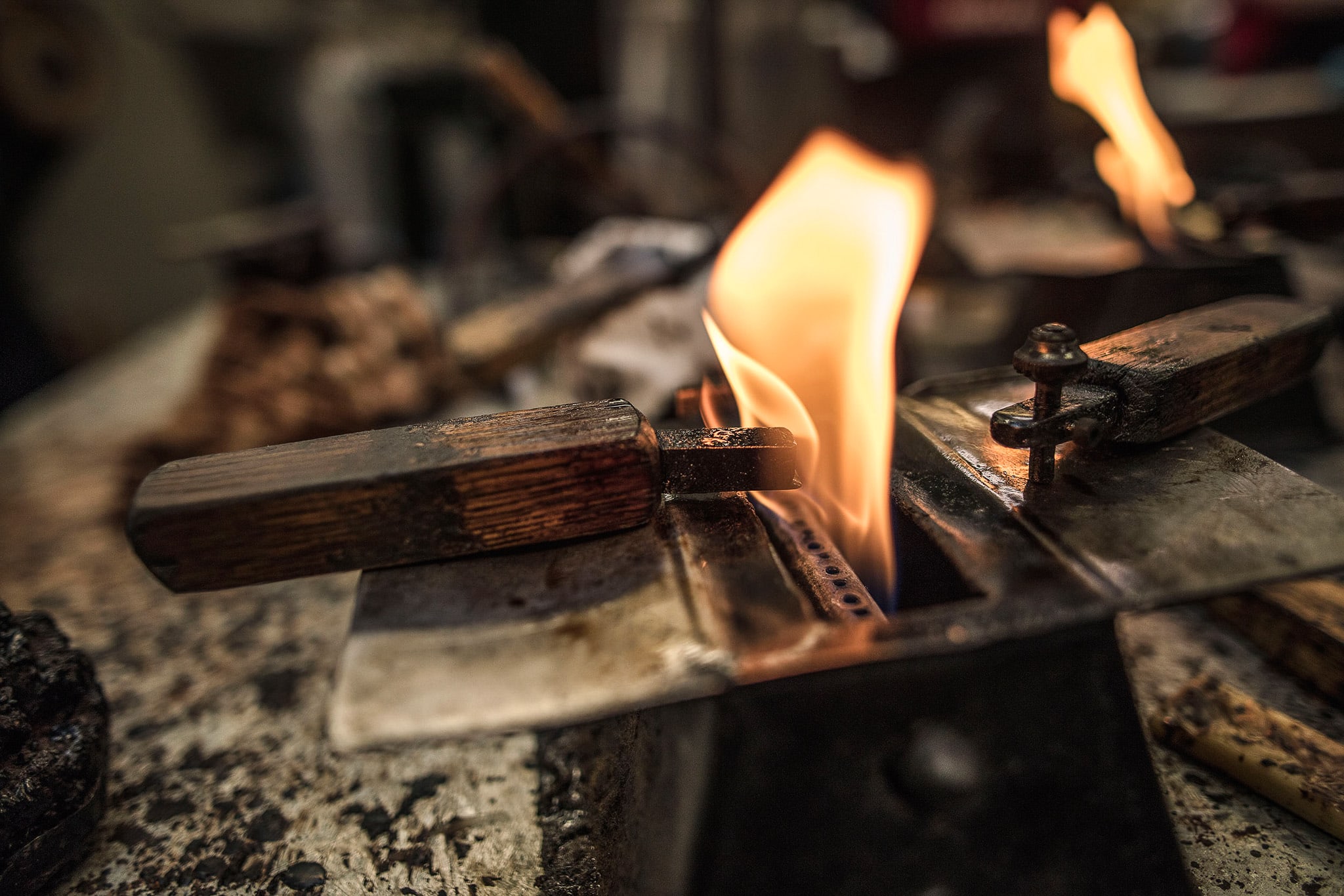
Ultime étape, le contrôle final. L’oeil scrupuleux des experts ne laisse naturellement rien passer, il en va de la réputation de la maison. Une à deux paires sur cent en moyenne se voient recalées. Une trace indésirable sur le cuir ici, un ajustement approximatif là. « D’infimes imperfections qui, le plus souvent, passeraient totalement inaperçues aux yeux du consommateur final mais qui n’atteignent pas le niveau d’excellence que nous nous imposons », confirme James Fox, le gendre du directeur général, lui aussi actif dans l’entreprise aux côtés de son épouse.
Une qualité qui fait le succès de la marque, comme le confirment Emer et Gary Lévy de la boutique Brogue à Genève: « De nombreux clients, de plus en plus sensibles à la manière dont sont élaborés les produits, nous demandent si les souliers que nous proposons sont confectionnés à la main. Dans le cas de Crockett & Jones, nous leur décrivons le processus de fabrication qui respecte et perpétue les savoir-faire traditionnels. Acquérir un produit unique - il n’y a pas deux paires strictement identiques - et authentique est une vraie satisfaction pour beaucoup d’entre-eux. »
Si le nombre de manufactures a chuté ces dernières décennies à Northampton, nul doute que celles qui subsistent et conjuguent intelligemment passé et présent ont de l’avenir.